Das Drahterodieren ist eine Schlüsseltechnologie im Maschinenbau und Werkzeugbau, die für ihre Präzision und Fähigkeit, komplexe Formen zu bearbeiten, bekannt ist. Dieser Blogbeitrag beleuchtet die Grundlagen und technischen Details des Drahterodierens, seine Anwendungen sowie die Rolle der A+N | POTT GmbH als Spezialist in diesem Bereich. Mit einer ISO 9001 Zertifizierung und einem starken Fokus auf kundenspezifische Lösungen setzt die A+N | POTT GmbH Standards in Qualität und Zuverlässigkeit. Erfahren Sie, wie das Unternehmen mit modernster Technologie und umfassender Expertise die Anforderungen seiner Kunden erfüllt.
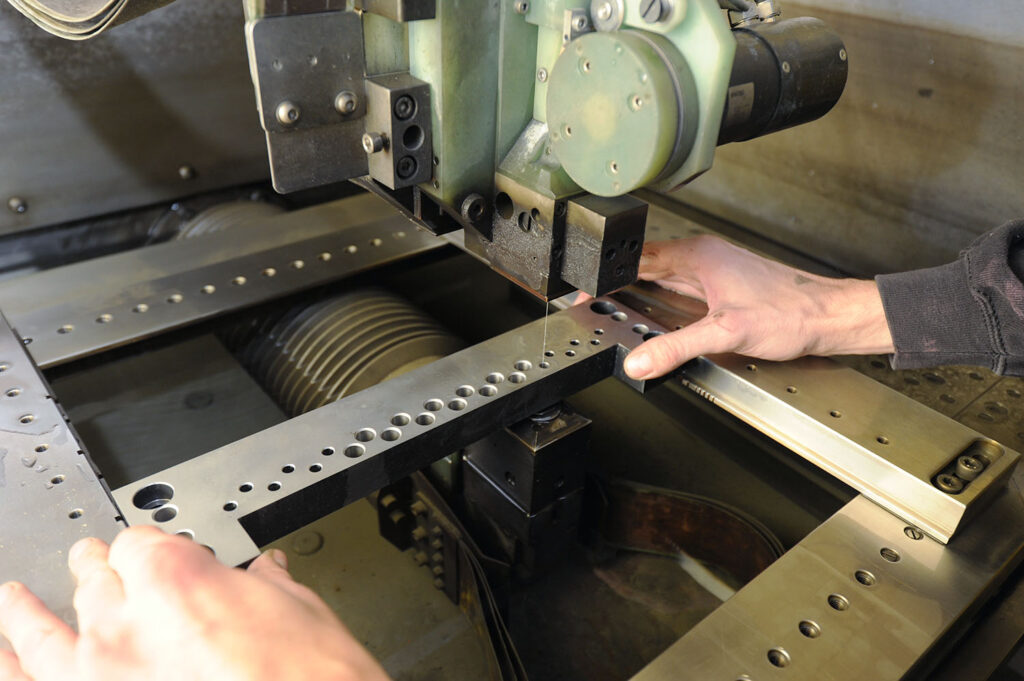
Inhaltsverzeichnis
Drahterodieren, auch bekannt als Funkenerosion mittels Draht, ist ein elektrothermisches Abtragungsverfahren, das sich besonders für die Bearbeitung von harten Materialien oder komplexen Formen eignet, die mit herkömmlichen Verfahren schwer zu bearbeiten sind. Das Grundprinzip basiert auf dem gezielten Abtrag von Material durch elektrische Entladungen (Funken) zwischen einem durch das Werkstück geführten Draht und dem Werkstück selbst. Der Draht fungiert als Elektrode und ist meist aus Messing, Wolfram oder Molybdän und wird manchmal noch mit einer dünnen Zinkbeschichtung versehen, was eine hohe Präzision und feine Schnittbreiten ermöglicht. Durch den Einsatz von deionisiertem Wasser als Dielektrikum werden die abgetragenen Partikel aus dem Schnittspalt gespült, was eine saubere und präzise Bearbeitung ermöglicht.
Definition und Grundprinzip des Drahterodierens
Flachschleifen ist ein Abrichtprozess, bei dem ein Schleifkörper in Form einer Scheibe oder eines Schleifsegmentes verwendet wird, um von einem Werkstück Material abzutragen. Ziel ist es, eine hohe Oberflächengüte zu erreichen sowie Maß- und Formgenauigkeit zu gewährleisten. Das Verfahren zeichnet sich durch seine Fähigkeit aus, sowohl harte als auch weiche Materialien mit großer Präzision bearbeiten zu können. Moderne Flachschleifmaschinen bieten eine Vielzahl von Einstellungsmöglichkeiten, um die Geschwindigkeit, den Anpressdruck und den Abtrag des Schleifmittels genau zu steuern, was für die Erreichung der gewünschten Oberflächenqualität und Toleranzen entscheidend ist.
Die Geschichte des Drahterodierens: Von den Anfängen bis heute
Die Wurzeln des Drahterodierens reichen zurück bis in die 1940er Jahre, als die Grundlagen der Funkenerosion erstmalig erforscht und entwickelt wurden. Die eigentliche Technik des Drahterodierens, wie wir sie heute kennen, begann jedoch erst in den 1960er Jahren Form anzunehmen, als die ersten kommerziell nutzbaren Maschinen auf den Markt kamen. Seitdem hat sich die Drahterodiertechnologie ständig weiterentwickelt und verfeinert. Die Einführung computergesteuerter CNC-Systeme in den 1970er Jahren markierte einen bedeutenden Fortschritt, der eine noch präzisere Steuerung des Erodierprozesses ermöglichte. Heute ist das Drahterodieren eine hochentwickelte Technik, die in vielen Industriebereichen unverzichtbar ist, insbesondere in der Herstellung komplexer Komponenten für die Luft- und Raumfahrt, die Medizintechnik und den Werkzeugbau. Mit der kontinuierlichen Verbesserung der Steuerungstechnik, der Materialwissenschaften und der Prozesseffizienz bleibt das Drahterodieren an der Spitze der Fertigungstechnologien, indem es Lösungen für die anspruchsvollsten Bearbeitungsaufgaben bietet.
Das Drahterodieren steht für eine hochpräzise Bearbeitungsmethode, die besonders bei der Fertigung von komplizierten Konturen und feinen Schnitten in harten Materialien zum Einsatz kommt. Aber wie genau funktioniert dieses Verfahren, und welche Materialien lassen sich damit bearbeiten? In den folgenden Abschnitten wird der Drahterodierprozess detailliert erklärt und ein Überblick über die verwendbaren Materialien und Werkstücke gegeben.
Der Drahterodierprozess Schritt für Schritt erklärt
Neben den Standardmodellen gibt es spezialisierte Kappmesser, die für spezifische Industriezweige entwickelt wurden. Diese Messer berücksichtigen die besonderen Anforderungen von Materialien und Prozessen. Beispielsweise werden in der Lebensmittelindustrie Kappmesser mit rostfreien Stahlqualitäten eingesetzt, die eine einfache Reinigung und Widerstandsfähigkeit gegen Korrosion bieten. In der Textilindustrie hingegen finden ultraleichte und extrem scharfe Messer Verwendung, um die Fasern präzise und mit minimaler Kraftanwendung zu schneiden. Diese spezialisierten Messer sind oft mit speziellen Beschichtungen versehen, die ihre Lebensdauer verlängern und ihre Leistung in anspruchsvollen Umgebungen verbessern.
Der Drahterodierprozess kann in mehrere grundlegende Schritte unterteilt werden, die zusammen ein außergewöhnlich präzises und effizientes Bearbeitungsverfahren bilden:
- Vorbereitung des Werkstücks und des Drahts: Zunächst wird das Werkstück so in der Maschine fixiert, dass es während des Bearbeitungsprozesses stabil bleibt. Der Draht, der als Schneidwerkzeug dient, wird, aufgewickelt auf einer Spule – wie eine endlose Elektrode – in die Maschine eingespannt.
- Einstellung der Parameter: Vor Beginn des eigentlichen Erodierens müssen verschiedene Parameter wie Spannung, Stromstärke und die Pulsfrequenz der Funkenentladungen eingestellt werden. Diese Parameter hängen von der Art des Materials, der Dicke des Werkstücks und der gewünschten Schnittqualität ab.
- Start des Erodierprozesses: Der Draht wird elektrisch geladen und bewegt sich in einem kontrollierten Abstand zum Werkstück. Durch die elektrischen Entladungen (Kurzschluss) zwischen Draht und Werkstück wird Material abgetragen (abgeschmolzen), ohne dass es zu einem direkten Kontakt kommt.
Kontinuierliche Spülung: Während des Erodierens wird das Bearbeitungsfeld kontinuierlich mit deionisiertem Wasser gespült. Dies dient dazu, die abgetragenen Metallpartikel wegzuspülen und eine Überhitzung des Werkstücks zu verhindern.
- Nachbearbeitung und Reinigung: Nach Abschluss des Erodierprozesses wird das Werkstück aus der Maschine entnommen und einer gründlichen Reinigung unterzogen. Eventuell notwendige Nachbearbeitungsschritte werden durchgeführt, um die endgültige Präzision und Oberflächengüte zu erreichen.
Materialien und Werkstücke im Drahterodierverfahren
Das Drahterodieren steht für eine hochpräzise Bearbeitungsmethode, die besonders bei der Fertigung von komplizierten Konturen und feinen Schnitten in harten Materialien zum Einsatz kommt. Aber wie genau funktioniert dieses Verfahren, und welche Materialien lassen sich damit bearbeiten? In den folgenden Abschnitten wird der Drahterodierprozess detailliert erklärt und ein Überblick über die verwendbaren Materialien und Werkstücke gegeben.

Der Drahterodierprozess Schritt für Schritt erklärt
- Vorbereitung des Werkstücks und des Drahts: Zunächst wird das Werkstück so in der Maschine fixiert, dass es während des Bearbeitungsprozesses stabil bleibt. Der Draht, der als Schneidwerkzeug dient, wird, aufgewickelt auf einer Spule – wie eine endlose Elektrode – in die Maschine eingespannt.
- Einstellung der Parameter: Vor Beginn des eigentlichen Erodierens müssen verschiedene Parameter wie Spannung, Stromstärke und die Pulsfrequenz der Funkenentladungen eingestellt werden. Diese Parameter hängen von der Art des Materials, der Dicke des Werkstücks und der gewünschten Schnittqualität ab.
- Start des Erodierprozesses: Der Draht wird elektrisch geladen und bewegt sich in einem kontrollierten Abstand zum Werkstück. Durch die elektrischen Entladungen (Kurzschluss) zwischen Draht und Werkstück wird Material abgetragen (abgeschmolzen), ohne dass es zu einem direkten Kontakt kommt.
- Kontinuierliche Spülung: Während des Erodierens wird das Bearbeitungsfeld kontinuierlich mit deionisiertem Wasser gespült. Dies dient dazu, die abgetragenen Metallpartikel wegzuspülen und eine Überhitzung des Werkstücks zu verhindern.
- Nachbearbeitung und Reinigung: Nach Abschluss des Erodierprozesses wird das Werkstück aus der Maschine entnommen und einer gründlichen Reinigung unterzogen. Eventuell notwendige Nachbearbeitungsschritte werden durchgeführt, um die endgültige Präzision und Oberflächengüte zu erreichen.
A+N | POTT GmbH:
Ihr Experte für im Flachschleifen aus Remscheid
Wenn Sie sich selbst von der Qualität und Präzision unserer Flachschleifdienstleistungen überzeugen möchten, dann kontaktieren Sie uns jetzt! Besuchen Sie unsere Website, rufen Sie uns an oder senden Sie uns gerne eine E-Mail. Erfahren Sie, wie wir mit maßgeschneiderten Lösungen Ihre Anforderungen im Flachschleifen erfüllen können!
Das Drahterodieren ist eine hochpräzise Fertigungsmethode, die eine Vielzahl technischer Aspekte und Feinheiten beinhaltet. Zwei zentrale Faktoren, die die Qualität und Effizienz des Erodierprozesses maßgeblich beeinflussen, sind die Komponenten der Erodiermaschinen und die Auswahl des Drahtmaterials. Diese Elemente spielen eine entscheidende Rolle in der Erzielung der gewünschten Präzision und Oberflächengüte der Werkstücke.
Wichtige Maschinenkomponenten und deren Funktionen
Ein Drahterodiergerät besteht aus mehreren Schlüsselkomponenten, die zusammenarbeiten, um eine präzise und effiziente Materialbearbeitung zu gewährleisten:
Die Drahtführung: Sie hält den Draht präzise auf seiner Bahn und gewährleistet eine genaue Schnittführung. Moderne Maschinen verfügen über hochentwickelte Drahtführungssysteme, die auch bei sehr feinen Drahtdurchmessern und komplexen Schnittmustern eine herausragende Präzision ermöglichen.
Die Stromversorgungseinheit (Generator): Sie erzeugt die für den Erodierprozess notwendigen elektrischen Entladungen. Die Qualität des Generators ist entscheidend für die Effizienz des Materialabtrags und die Minimierung von Drahtbrüchen.
Das Dielektrikum-Management-System: Typischerweise wird deionisiertes Wasser als Dielektrikum verwendet, das den Bereich zwischen Draht und Werkstück flutet. Das Management-System steuert die Filtration, Temperierung und Zirkulation des Dielektrikums, um optimale Bearbeitungsbedingungen sicherzustellen.
Die CNC-Steuerung: Die computergesteuerte Programmierung ermöglicht die präzise Steuerung des Drahterodierprozesses, einschließlich der Drahtbewegung und der Prozessparameter. Fortgeschrittene Steuerungssysteme bieten umfangreiche Möglichkeiten zur Optimierung des Erodierprozesses.
Auswahl des Drahtmaterials und dessen Einfluss auf die Präzision
Die Auswahl des Drahtmaterials ist ein weiterer kritischer Aspekt, der die Präzision, Schnittgeschwindigkeit und Oberflächengüte des fertigen Werkstücks beeinflusst. Die häufigsten Materialien für den Erodierdraht umfassen:
Messing: Ein weit verbreitetes Material, das eine gute Balance zwischen Kosten, Schnittgeschwindigkeit und Präzision bietet. Es eignet sich für eine breite Palette von Anwendungen.
Beschichteter Draht: Draht, der mit einer dünnen Schicht eines anderen Materials (z.B. Zink) beschichtet ist, kann die Schnittgeschwindigkeit erhöhen und die Oberflächengüte verbessern. Diese Drähte sind ideal für Anwendungen, bei denen es auf höchste Präzision ankommt.
Molybdändraht: Wegen seiner hohen Zugfestigkeit und geringeren Dehnung ist Molybdändraht besonders geeignet für Anwendungen, die extrem feine Schnitte erfordern.
Die Wahl des Drahtmaterials hängt von den spezifischen Anforderungen der zu bearbeitenden Werkstücke und der gewünschten Endqualität ab. Fortschritte in der Materialwissenschaft haben zu einer ständigen Verbesserung der Drahtqualität geführt, was wiederum die Leistungsfähigkeit des Drahterodierens erhöht.
Die A+N | POTT GmbH zeichnet sich durch eine Reihe von Merkmalen aus, die sie von anderen Anbietern im Markt abheben:
Umfassende Expertise: Mit einem Team aus hochqualifizierten Fachkräften und Ingenieuren verfügt A+N | POTT über umfangreiches Know-how in der Drahterodiertechnik. Dieses Wissen ermöglicht es dem Unternehmen, auch die anspruchsvollsten Projekte mit höchster Präzision zu realisieren.
Qualitätsversprechen: Qualität steht im Mittelpunkt aller Prozesse bei A+N | POTT. Durch die Verwendung hochwertiger Materialien, modernster Maschinen und präziser Messinstrumente gewährleistet das Unternehmen erstklassige Ergebnisse bei jedem Auftrag.
Kundenorientierung: Die A+N | POTT GmbH versteht die einzigartigen Anforderungen jedes Kunden. Durch enge Zusammenarbeit und Beratung werden maßgeschneiderte Lösungen entwickelt, die exakt auf die Bedürfnisse und Spezifikationen der Kunden abgestimmt sind.
Zuverlässigkeit und Termintreue: In der schnelllebigen Welt der Fertigung sind Zeit und Zuverlässigkeit entscheidend. Die A+N | POTT GmbH ist bekannt für seine Pünktlichkeit und die Einhaltung von Lieferfristen, was das Unternehmen zu einem verlässlichen Partner in Projekten jeglicher Größe macht.
ISO 9001 Zertifizierung: Ein besonderes Qualitätsmerkmal der A+N | POTT GmbH ist die ISO 9001 Zertifizierung, die das Engagement für höchste Standards in Qualitätsmanagement und Kundenzufriedenheit belegt.
Die ISO 9001 Zertifizierung unterstreicht die systematischen Ansätze und die kontinuierliche Verbesserung aller Prozesse bei der A+N | POTT GmbH. Für Sie als Kunden bedeutet diese Zertifizierung Sicherheit und Vertrauen in alle Dienstleistungen und Produkte von uns, da sie garantiert, dass ihre Projekte nach international anerkannten Qualitätsstandards abgewickelt werden.
Das Streben nach Innovation und technologischer Führung ist ein zentraler Pfeiler der Philosophie von A+N | POTT GmbH. Dies manifestiert sich in der kontinuierlichen Investition in die neueste Drahterodiertechnologie sowie in der Entwicklung individueller Lösungen für die Kunden:
State-of-the-Art Technologie: A+N | POTT setzt auf die modernsten Drahterodiermaschinen und Softwarelösungen, um präzise und effiziente Bearbeitungsprozesse zu gewährleisten. Dies ermöglicht das Unternehmen, mit den neuesten Trends und Anforderungen der Branche Schritt zu halten.
Individuelle Kundenlösungen: Jedes Projekt wird bei A+N | POTT als einzigartig betrachtet. Das Unternehmen spezialisiert sich darauf, individuelle Lösungen zu entwickeln, die genau auf die spezifischen Anforderungen und Herausforderungen jedes Kunden zugeschnitten sind. Von der ersten Idee bis zum fertigen Produkt begleitet A+N | POTT seine Kunden mit Fachexpertise und maßgeschneiderter Beratung.
Engagement für Exzellenz: Die Kombination aus erfahrenen Mitarbeitern, modernster Technik und einem starken Fokus auf Kundenbedürfnisse macht A+N | POTT GmbH zu einem führenden Unternehmen im Bereich Drahterodieren. Ihr Engagement für Exzellenz in jedem Aspekt ihrer Arbeit sichert den Kunden nicht nur herausragende Ergebnisse, sondern auch einen unschätzbaren Mehrwert für ihre Projekte.
Die A+N | POTT GmbH in Remscheid steht für Qualität, Zuverlässigkeit und Innovation im Bereich des Drahterodierens. Mit individuellen Lösungen, die auf die neueste Technik abgestimmt sind, bieten wir unseren Kunden einen unvergleichlichen Service, der die Grundlage für langfristige Partnerschaften und erfolgreiche Projekte bildet.
Sie sind auf der Suche nach einem zuverlässigen Partner für das Drahterodieren? Dann kontaktieren Sie uns jetzt ganz unverbindlich!
Warum die A+N | POTT GmbH als Ihr Partner für Drahterodieren?
Die A+N | POTT GmbH ist Ihr verlässlicher Partner für Drahterodieren, dank umfassender Expertise und modernster Technologie. Unsere hochpräzisen Maschinen und qualifizierten Fachkräfte ermöglichen es uns, selbst komplexeste Werkstücke mit höchster Genauigkeit zu bearbeiten. Wir bieten maßgeschneiderte Lösungen, die individuell auf Ihre Bedürfnisse abgestimmt sind und höchste Qualität garantieren. Durch kontinuierliche Innovation und strenge Qualitätskontrollen sichern wir die Effizienz und Präzision Ihrer Produktionsprozesse.
Beitrag der A+N | POTT GmbH zur Innovation und Qualitätssicherung in der Branche
Die A+N | POTT GmbH leistet einen entscheidenden Beitrag zur Innovation und Qualitätssicherung in der Branche durch ständige Weiterentwicklung und den Einsatz modernster Technologien. Unser Engagement für Spitzenleistung zeigt sich in der kontinuierlichen Optimierung unserer Produktionsprozesse und der Einführung fortschrittlicher Fertigungsmethoden. Wir setzen auf umfassende Schulungen und Weiterbildung unserer Mitarbeiter, um höchste Qualitätsstandards sicherzustellen.
Qualitätsmanagement bei der A+N | POTT GmbH
Die A+N | POTT GmbH hebt sich in der Branche durch ihre Verpflichtung zu Qualität und kontinuierlicher Verbesserung hervor, was durch die DIN ISO 9001 Zertifizierung unterstrichen wird. Diese Zertifizierung ist ein weltweit anerkannter Standard, der Anforderungen an ein effektives Qualitätsmanagementsystem stellt. Bei A+N | POTT gewährleistet die Einhaltung der DIN ISO 9001 Normen, dass sämtliche Prozesse, von der Entwicklung bis zur Endfertigung systematisch überwacht und optimiert werden.
